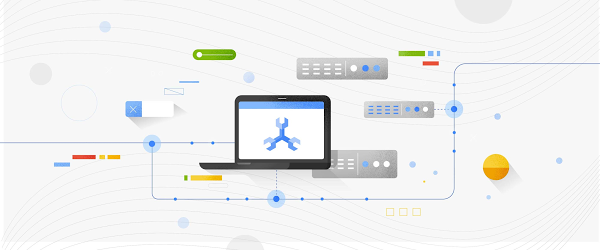
Testing Dataflow pipelines with the Cloud Spanner emulator
May 24, 2021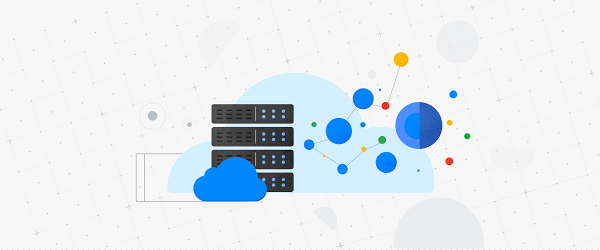
VM Manager simplifies compliance with OS configuration management Preview
May 24, 2021The U.S. Navy spends billions annually to fight rust and corrosion on its ships. Of course, this is to be expected given its vessels are largely made of steel. However, inspections of ships, aircraft and vehicles are a time-consuming and critical part of keeping the U.S. Navy at top performance.
To address this issue, Google Cloud and Simple Technology Solutions (STS)—a Google Cloud partner and 8a HUBZone small business specializing in cloud solutions for the federal government—successfully completed the first phase of its project to help identify rust and corrosion in hard-to-reach places of ships, funded by the Department of Navy (DON) Small Business Innovation Research program. With the successful completion of phase one, STS and Google Cloud teams are now kicking off its second phase.
In the first phase, STS built a corrosion detection and analysis solution using Google Cloud’s artificial intelligence/machine learning (AI/ML) platform. Leveraging Google’s native computer-vision capabilities and commercial drones, the team successfully identified “corrosion of interest” in aerial images of vessels, with confidence scores of more than 90% with very few false positives. This was an engineering feat that required complex integration between emerging software and hardware technologies.
Phase two of the project aims to achieve the same corrosion detection capability across any required platform. As such, the solution will be expanded to include aircraft, buildings, bridges, and other infrastructure across the Department of Defense (DoD), and other commercial verticals, like oil and gas, construction, and maritime shipping.
With commercialization and speed-to-market being the priority, STS will also add a front-end user interface (UI) to the solution in phase two. The UI will include interactive 3D models of the platform to map detection of severe corrosion to the exact location on the vessel or aircraft. This will allow inspectors to use the solution independently in the field and best prioritize where they spend their time.
“The objective for the project was not only intended for ships, aircraft, or vehicles, but also to truly transcend all forms of corrosion across industries,” said Steve McKee, lead for DON’s Naval Enterprise Sustainment Technology Team. “The corrosion problem is not unique to the Navy, or to the Department of Defense. There are ramifications for the defense industry, maritime shipping, aviation, mining, and more. There are countless sectors for which this solution will have a resounding impact. We believe the entire defense ecosystem will benefit.”
Expanding AI / ML platform detection and analysis capabilities is a complex engineering challenge and will require extensive new data collection, expanded sensor capabilities, and new algorithms, including:
-
New data collection: STS is partnering with DroneUp, a commercial drone flight services company, to collect new platform corrosion images using semi-autonomous drones. In addition to automating data collection, DroneUp will show the interiors of vessels and tanks—not just the exterior. Several groups within the Department of the Navy, the Department of the Air Force, and other federal agencies are contributing a trove of corrosion data across platforms to expedite training the new models. This collaboration is a testament to the pervasiveness of the corrosion detection and inspection challenges.
-
Expanded sensor capabilities:Images and RGB color model and camera sensors data are not sufficient to detect corrosion on all platforms. For example, infrared or multi-spectral sensors are required for aircraft, as thick coats of paint typically cover the corrosion, making it invisible to the naked eye. Similarly, submarines and ships have anechoic tiles, or surfaces that are coated in rubber. An “ecosystem of sensor data” is required to achieve platform agnosticism and maximize commercialization potential.
-
New algorithms: New data technologies and models will be developed corresponding to the various sensor inputs and then fused with the solution. The existing model will also be enhanced to include a categorization schema to prioritize inspector activities.
This application of AI / ML combined with drone imagery showcases one of the many possibilities for this technology across the DoD and beyond. As this collaboration continues to phase two, Google Cloud and STS will continue to work toward ways to further expand this corrosion detection model, and ultimately improve the process for corrosion across all types of infrastructure.
To learn more about our solutions for the Federal Government, visit cloud.google.com/solutions/federal-government.